ELECTRIC VEHICLES
Electric vehicles are quite affordable as they have compact moving parts for maintenance and are also environment friendly as they use no fossil fuels. Some EV batteries need lead-acid or nickel-metal hydride batteries the standard for modern vehicles working on batteries is considered lithium-ion batteries since they last longer and are good at energy retention with efficient self-discharge rates. Despite such technological improvements some problems still occur such as fire or explosions in battery-based vehicles. To reduce such disasters we have introduced a new Battery Management System(BMS).
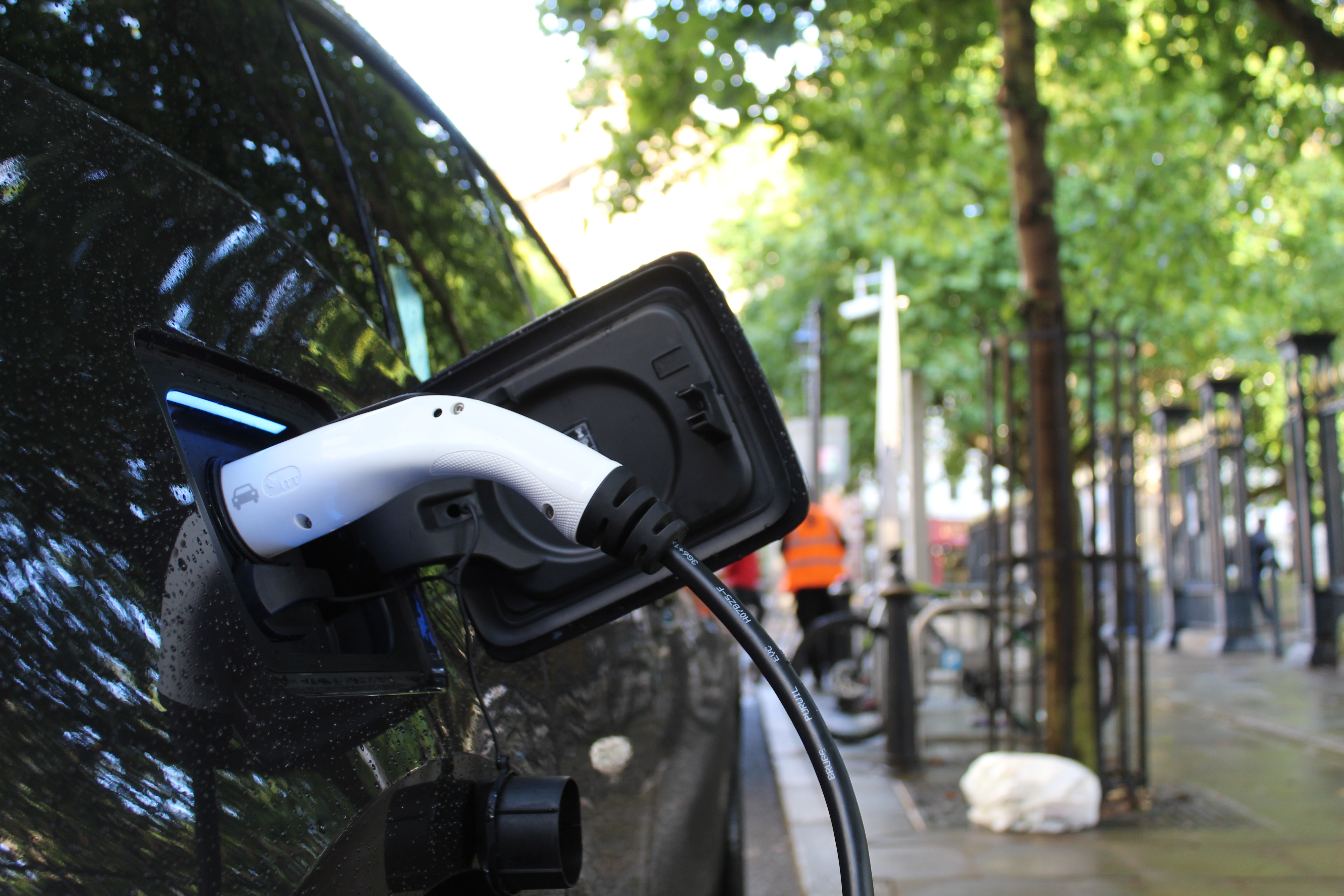
TYPES OF ELECTRIC VEHICLES
There are two main types of electric vehicles based on their working mechanisms.
- Battery Electric Vehicles
- Plug-In Hybrid Electric Vehicles
BATTERY ELECTRIC VEHICLES [BEV]
Some perks of using battery-based electric vehicles are they create less noise and hence less noise pollution, it has no exhaust, spark plugs, clutches, or gears, and doesn’t use any fossil fuel hence are nature friendly. It can also be charged at home overnight which provides enough power for the journey. Though longer journeys or ones with more elevation are a bit harder even with fully charged batteries. The charging time of vehicles ranges from 30 minutes to 12 hours and this variation depends on the speed of the charging station and the sizes of the batteries.
PLUG-IN HYBRID ELECTRIC VEHICLES [PHEV]
Such vehicles don’t entirely depend on electric motors but have hybrid systems which have combinations of batteries as well as fossil fuel. Journey on such vehicles is more reliable for longer distances as we can switch to fossil fuels even if batteries are discharged. But these vehicles have their own disadvantages same as those combustion engine vehicles such as hectic maintenance, engine noise, cost of fossil fuels, and emission
BATTERY MANAGEMENT SYSTEM
With our proprietary smart BMS comparable to a magnum opus, be assured that you won’t have the misfortune of having to use your EV as a smoke machine in your music concert.
As we see there is a sudden rise in the EV market, here safety should be our utmost priority to enjoy the ride with a safe vehicle. Due to the persistent surveillance of the battery pack, it ensures the smooth functioning of the battery and avoids overheating the battery. BMS keeps a check on the temperature and voltage of every cell in the battery pack. Such systems make it easy to track precisely where the problem is and the main reason behind it which doesn’t lead to catastrophic failure and prevents it. The battery pack is just a small device with spontaneous combustion which when have a small puncture in the cell which leads to huge battery discharge and may result in fire.
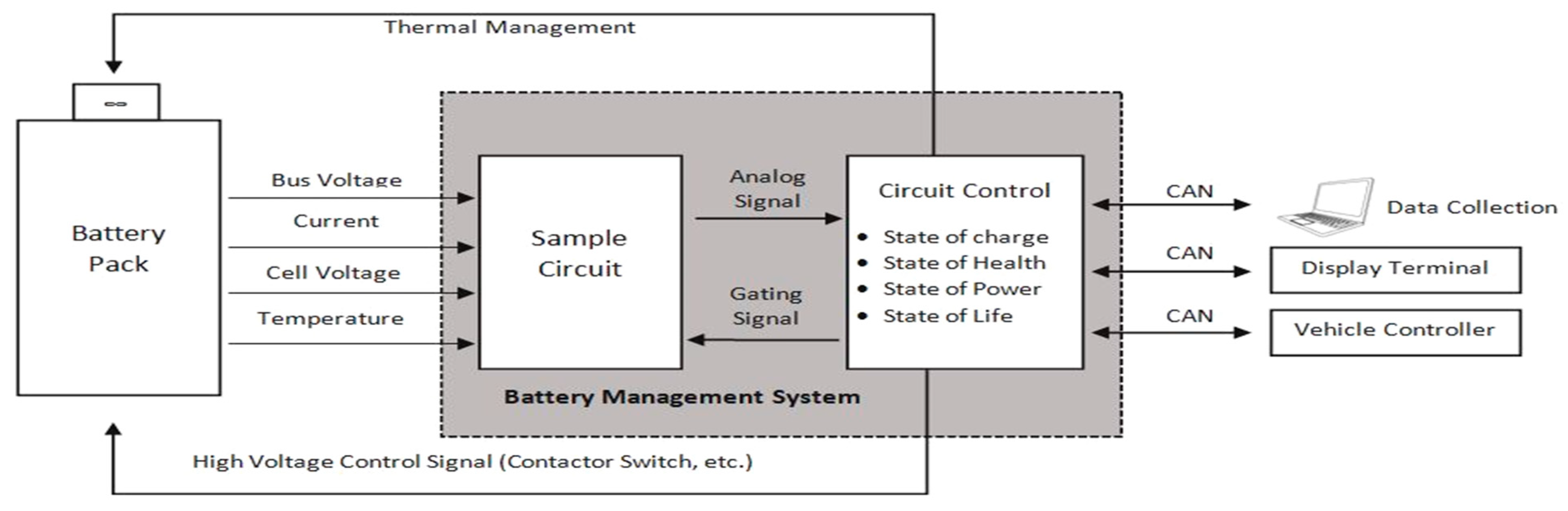
MECHANISM OF BATTERY MANAGEMENT SYSTEM
The key function of the Battery Management System(BMS) is keeping a check on the hazardous battery pack, which is to monitor charging and discharging cells. Battery Management System(BMS) is a set of circuits that are designed to carry out this task. The microcontroller of the integrated circuits has inbuilt algorithms which maintain the smooth working of cells and can also be called the brain of the system. The battery has sensors placed inside it that report the cell temperature and voltage of each cell to the system. BMS is a system with a smooth flow that helps to keep values under desirable ranges.
CHARGING OF BATTERY
Lithium batteries are generally charged with constant current till the cell reaches a voltage of 4.2V. As the charging continues the voltage is kept constant throughout the charging process. Later the charger switches off the charging process either when the least current or after the preset time is reached. There is a protection circuit or passive safety element on the cell incase if charging continues the flow of current even after the maximum limit is reached. Such safety elements are brought into use to ensure battery and user security at times.
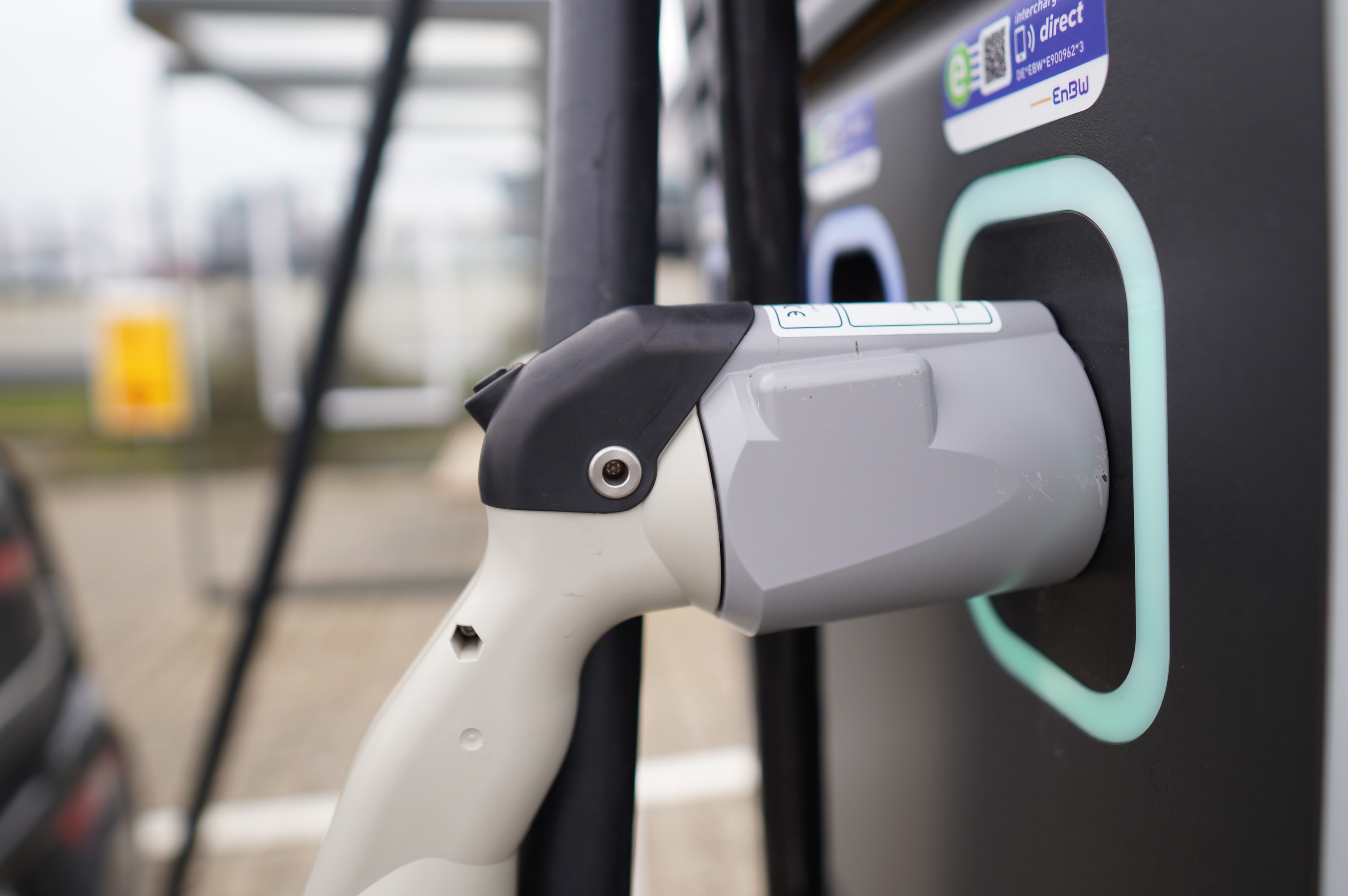
OVERCHARGING
Have you ever wondered what happens when a battery is overcharged?
It is advised not to overcharge batteries in order to operate them safely and increase their life span. Since the battery is overcharged more and more energy tries to enter the cells which results in rising in voltage level. Such situations and phenomena are harmful to the battery and bad for the battery life also they cause risk for the users. Too much energy leads to rising temperature and heat generation. In extreme cases, excessive heat generation leads to thermal runways, which means due to rising temperature cells start making chemical changes inside it which expand exponentially. And such things lead to fire or explosions in the battery.
OVERCHARGING WITH BATTERY MANAGEMENT SYSTEM
The Battery Management System helps in avoiding the overcharging of cells. Cells when overcharged gain higher energy value which is not desirable and harmful to the system. The extra energy provokes the cells to increase temperature and so it causes the breakdown of cell chemistry which is not ideal for the system. Since the cells are overcharged they swell up and have a higher risk of getting exploded additionally due to the higher temperature risk of fire increases as well. Hence, overcharging cells is extremely dangerous for battery life even if it doesn’t catch fire.

CELL BALANCING
This System has many various features, one of which is the cell balancing function. The battery pack contains several cells, making it difficult to maintain the same voltage during the manufacturing process. Sometimes the voltages of a few cells are imbalanced and have either lower voltages or higher voltages than the desirable range. But this doesn’t tend to be risky in the case of BMS as it cuts off the power whenever the lower potentials reach the Undervoltage threshold. Let’s assume an example with a pack of 100 cells and a single cell having the potential of 3V whereas the rest all have 3.5V of potential. So during the normal operations consider the cells getting discharged at a constant rate but the cell with lower potential would reach the Undervoltage threshold earlier than the rest of the cells and there is a power cutoff by BMS now.
The higher potential cells would reach the charge threshold earlier than the lower ones, which means when the ones with 3.5V would reach 4.2V, those with lower potential 3V would be at 3.7V. The battery pack would not work at its full potential with imbalanced cells resulting in frequent charging and a reduced range and battery life.
HOW TO AVOID DAMAGE
Well, here’s the part where the cell balancing function comes into the picture. BMS tends to bring each cell voltage to the same desirable range and hence battery is brought in use to its full extent. Here the battery is used to the full extent and the risk of battery damage is reduced.
We know that replacing a battery now and then is a headache, isn’t it?
TYPES OF CELL BALANCING
Battery Management System which has a cell balancing feature is further classified into two types which are active balancing and passive balancing. The function of active balancing transfers the charge from higher potential cells to lower potential cells efficiently by inductive or capacitive charge shuffling. In passive balancing the cells with higher potentials are discharged and brought to the level of lower potential cells by dissipation of energy, this is generally carried out with the help of a resistor.

1. ACTIVE CELL BALANCING
Active cell balancers generally shift energy cells to sell, that is shifts energy from high voltage cells to the cells with lower voltages. The main motive of the balancer is to increase the life span by balancing the voltage level of all the cells in the battery. Rather than dissipating the energy in form of heat the balancers efficiently try to balance the cells which have small converter circuits which pass energy from higher voltage cells to lower-voltage cells. Active cell balancing is further classified into two types:
- Charge shuttling – This is used to transfer charge cell to cell actively resulting in equal voltages.
- Energy converters – It used transformers and inductors to transfer energy between cells of the battery pack.
ADVANTAGES OF ACTIVE CELL BALANCING
- This enhances capacity usage. Its performance is great when cell capacities are different and in series.
- Energy efficiency is increased and energy is saved rather than burning extra energy through shifting it to lower energy cells.
- The life expectancy of cells is increased.
- The balancing process is faster.
DISADVANTAGES OF ACTIVE CELL BALANCING
- The process of shifting energy from cell to cell loses approximately 10-20% energy.
- Charges are supposed to travel from higher cells to lower cells only.
- The control algorithm of the active cell balancer is more complex despite of being more efficient.
- It is not quite affordable as the production cost is more as all cells should be interconnected to each other.
2. PASSIVE CELL BALANCING
The passive system generally burns out extra energy from higher cells by a resisting element till the level is brought to lower ones. If there is a pack of cells in series it is noticed that energy in cells varies as some have low energy and others have comparatively higher. In series, arrangement cells can be easily balanced by attaching resistor which releases energy in heat form and the cells are balanced in energy pack.
Firstly the extra energy is burnt away unless there is a balance between all the cells. Passive cell balancing makes all cells appear with the same capacity. Passive cell balancing is further classified into two different types:
- Fixed shunting resistor – this circuit is generally connected to fixed shunting to avoid overcharging. Resistors help passive balancing circuits to control the level of every cell voltage without any damage. Energy used by such resistors to balance a battery may result in heat loss in the Battery Management System. It can be concluded that a fixed shunting resistor is an inefficient method for cell balancing.
- Switch shunting resistor – this switch shunting resistor method is quite common in cell balancing. It has a continuous mode and sensing mode, here in continuous mode every switch is controlled simultaneously and in sensing mode, every cell requires a real-time voltage sensor. This circuit is ideal for the system which uses low current when charged or discharged.
ADVANTAGES OF PASSIVE CELL BALANCING
- There is no need to balance a pack that works efficiently.
- The state of charge is the same with all cells.
- It has an affordable method of cell balancing.
DISADVANTAGES OF PASSIVE CELL BALANCING
- Thermal management is not proper.
- Balancing is done only through the top of every cell around 95%, as because of different cell capacities burning off excess energy is needed.
- The transmission of energy is generally slower. Electrical energy if usually dissipated as heat in resistors and the circuits account for the switching losses, in short, there is a high amount of energy loss.
- This system doesn’t enhance the run-time of a battery-powered system.